34+ Inventory Examples to Download
A simple inventory can come in many forms. However, inventories are commonly used by businesses so they can have a list of their available products, equipment, property, raw material stock, tools, and/or any other items present within the location of the business. There are also samples of trading inventory and content inventory which are used in different kinds of information listing.
Whether you would like to create your own free inventory template or you want to execute an inventory turnover, you can browse through and refer to our downloadable samples and templates of inventory documents available in this post.
Software Inventory Tracking Template
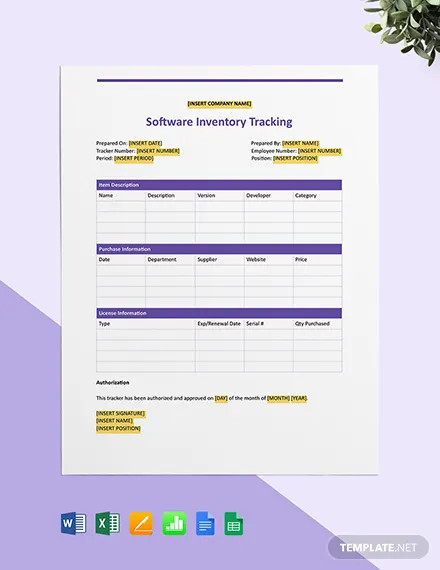
Restaurant Special Menu Inventory Template
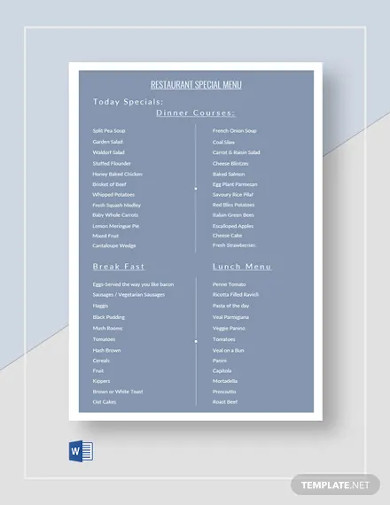
Inventory Report Template
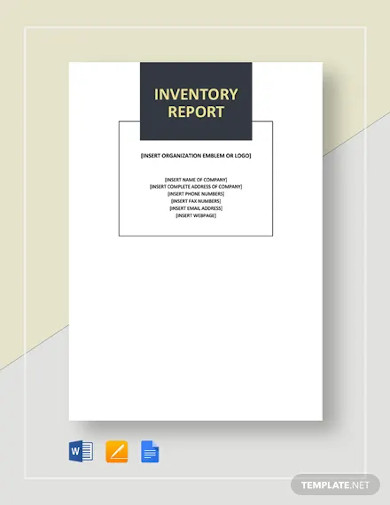
Perpetual Inventory & Ordering Template
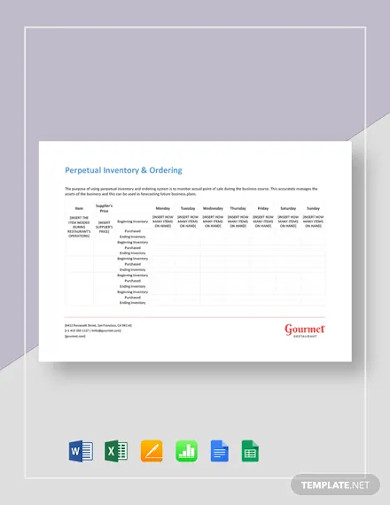
Food & Beverage Inventory Template
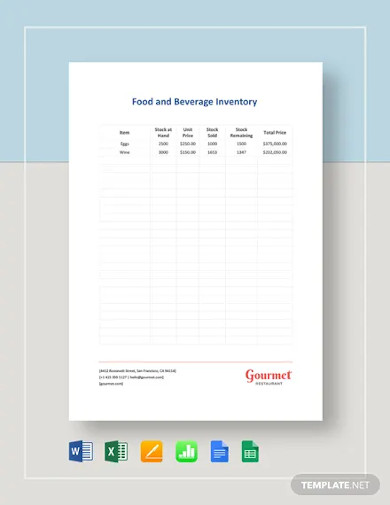
Inventory Count Sheet Template
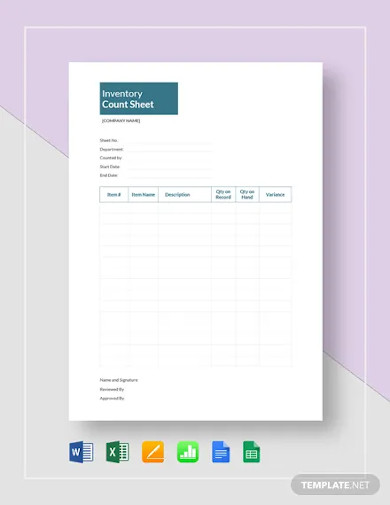
Inventory Checklist Template
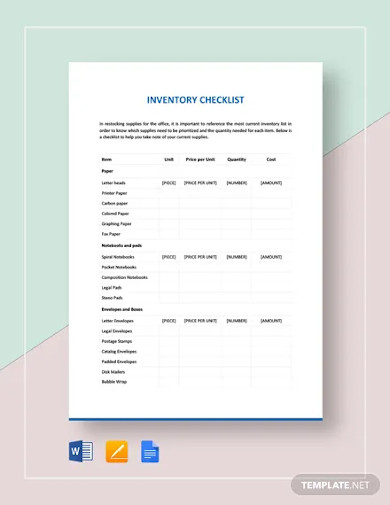
Inventory Sign Out Sheet Template
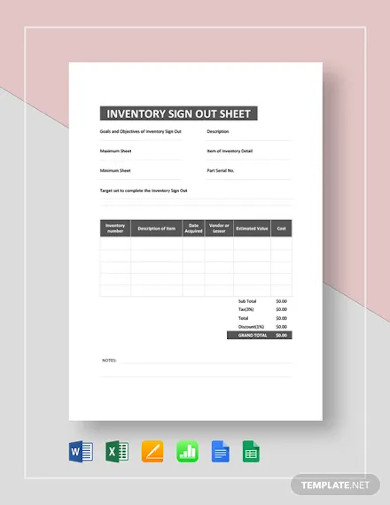
Product Inventory
Food Product Inventory
Health Product Inventory
Retail Product Inventory
Retail Inventory
Retail Store Inventory
Retail Grocery Inventory
What Is an Inventory?
There are a lot of ways that an sample inventory can be described. Here are some of the mostly used definition of an inventory:
- It is a list of the property of a company used for its operations and production.
- Free inventory examples are catalogs of the tangible goods that an entity owns.
- It is a record of the description of the items that an individual has which is relevant to his/her daily functions.
- It is a precise and itemized documentation of the consumables within the vicinity of the location of the business including merchandise, raw materials and finished goods.
- A inventory can also be used to specify a maintenance and repair listing of various items.
How to Create a List Inventory?
You can easily create a list inventory by following these steps:
- Be specific with the list inventory that you would like to create. Moving inventory, restaurant inventory or whatever inventory it is that you target to have, always itemize the things that you would like to include in an inventory document.
- Be specific in whether you will create inventory examples in Doc that are based on item groupings or you would like to create a general one.
- Open a software where you will create an list inventory. You can also use a readily made template so it will be easier for you to format the document.
- Create a list of the things within the inventory by row and create columns which may contain these headings:
- The number of pieces per item
- The description of the item
- The expiration of the item, if applicable
- The location where the items are stored
- The specific identification or bar number of the item present in the storage
- Review the list and identify if there are still items that have not been include in the list or if there are corrections that are needed to be made.
Stock Inventory Example
Blank Stock Inventory
Home Inventory
Data Inventory
Data Inventory Example
Personal Data Inventory
Equipment Inventory
Lab Equipment Inventory
Sound Equipment Example
Property Inventory
Personal Property Inventory
Rental Property Sample
Furnishing Property Inventory
Usages of Inventories
An inventory can be used by the following entities:
- A restaurant that needs to take note of their ingredients, food inventories, raw stocks, kitchen equipment and utensils
- An individual who wants to record his/her properties
- A business that needs to assure that they have a precise and accurate listing of the items within their storage
- An organization that requires a property inventory and other resources listing including the things present within the vicinity of their office
Some of the ways on how inventories are used by the above mentioned entities include the following:
- An inventory can be an asset inventory which contains the list of the things that are needed for the continuous transaction of the business may it be with other businesses or with its clients.
- Inventories in Excel are used by companies to make sure that they can have a precise list of the things that are still present within the different areas of the business premises.
- An inventory can serve as a signal when the resources or stock of the business is about to run out. This can help the management to replenish their supplies to avoid delays in operational procedures.
- Inventories are used to properly issue downtime, production issues, and other problems with regards to order purchases.
- Inventory listing can be of help as they assure that the raw materials of a business will be absorbed or used before date of expiry.
Computer Inventory
Computer Equipment Inventory
Free Computer Inventory
Liquor Inventory
Blank Liquor Inventory
Liquor Inventory Sample
Warehouse Inventory Example
Free Warehouse Inventory
Printable Warehouse Inventory
Dos and Don’ts in Creating and Using an Inventory
Listed below are some of the dos and don’ts that you should be mindful about if you will create or use an inventory may it be a skills inventory, a data inventory or any other kinds of inventory documents.
- Do use a sample inventory that is relevant to the operations of your business or organization. Using an inventory format which contains all the details that you need to know and how they will be used can help a lot in assuring the effectiveness of the usage of the inventory.
- Do list down items in the inventory based on your current stocks. Have a different listing of the items that you have already pulled out or the items that are about to be delivered in the location of your business. However, you can also create additional rows or columns in the retail inventory that you have if it will be more practical with the operations that your business have.
- Do not create an inventory that will only be used for a short period of time. For an instance, a home inventory example should be an essential tool that you will use for a long duration so you can track the updates and development that you have in terms of stock storage and usage.
- Do not allow people who are unaware of the inventory usage to edit the document when you are unable to do so. As much as possible, have a designated person or people who will use and put additional details to the inventory so it will be easier to know how data is being placed, changed or replaced in the document.
Restaurant Inventory
Restaurant Equipment Inventory
Restaurant Food Inventory
Content Inventory
Content Inventory Example
Supply Inventory Example
School Supply Inventory
Cleaning Supply Inventory
Food Inventory
Food Storage Inventory
Basic Food Inventory
What Is an Inventory Management?
Now that you are already aware of what an inventory is and how it is useful in different kinds of instances and operations, the next thing that you need to be aware of is the process of inventory management. An inventory management can be described as follows:
- It is the process of having a quality checklist usable in managing stocks or non-capitalized items that an entity possesses.
- An inventory management is away of filing and recording inventories that are used in different areas within a business location.
- Inventory management is a part of supply chain management which allows the business to have a checklist so they can be ready with the demands of the consumers while maintaining efficiency in supply storage, acquisition and assessment.
- Inventory management makes the business aware of the procedures that are needed to be done for items to be delivered from their manufacturers up to the warehouse or any storage area of the company.
- Inventory examples in PDF, Excel or Word which are being managed by specific divisions or departments of the company helps an organization in assuring that all the information within the specific inventories are accurate and updated.
Making an inventory is not enough. Assuring that it is well kept, organized and managed well is what makes the difference in relevance to the effectiveness of this document.