17+ Job Safety Analysis Examples to Download
As much as we’d all like to work in perpetually safe environments, that’s not really the case. There will be hazards from time to time, but companies must find ways to mitigate those for everybody’s benefit. To help out with that endeavor, it comes highly recommended that companies conduct their own job safety analysis from time to time. Learn more about it by scrolling down and check out what a top-notch job safety analysis template looks like from our list below.
Job Safety Analysis examples
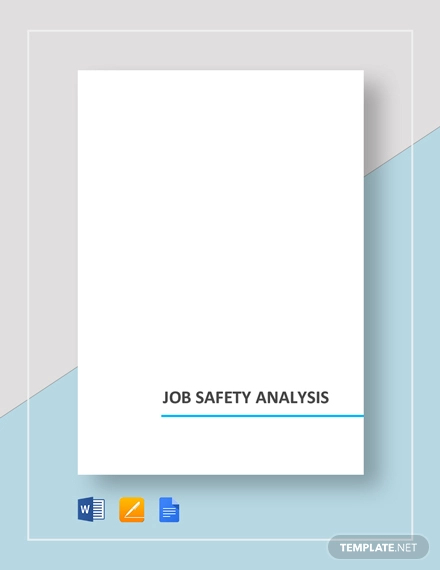
Job Safety Analysis Spreadsheet Template
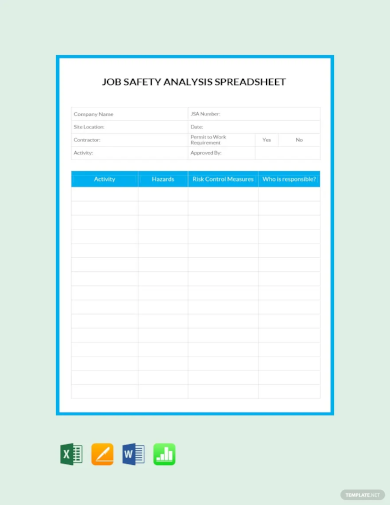
Job Analysis Gantt Chart Template
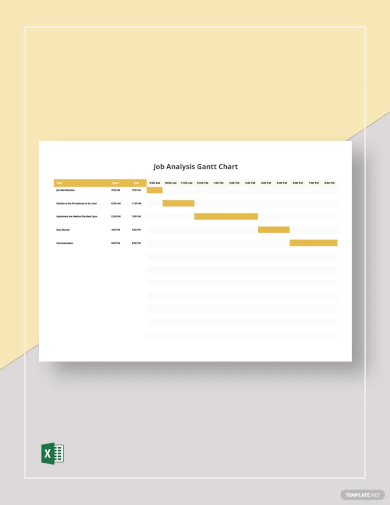
Safety Analysis Report Template
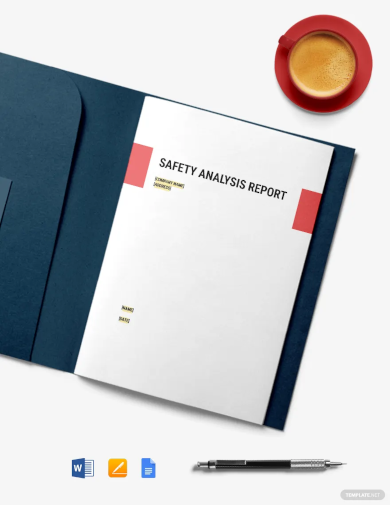
Job Analysis Report Template
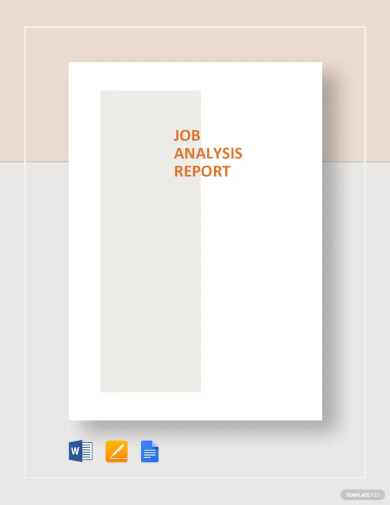
Job Safety Analysis Template
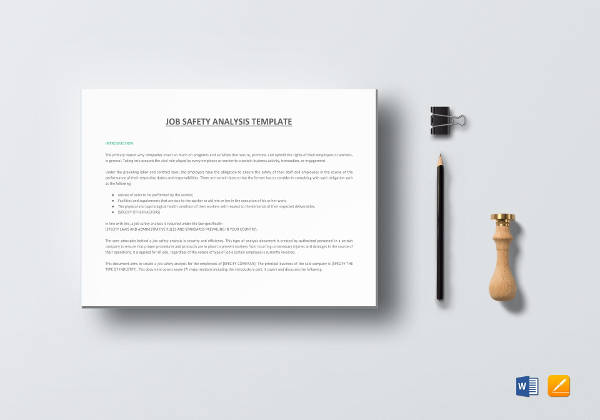
Job Safety Analysis Worksheet Example
Job Safety Analysis Worksheet Template
Job Safety Analysis Document Example
Task Specific Job Hazard Analysis
Sample Job Task Analysis Form
Job Safety Analysis Template
Field Level Job Risk Assessment
Job Hazard Identification Checklist
Job Safety Analysis Worksheet Document Example
Construction Risks Job Safety Analysis
Generic Job Safety Analysis Form
What Is a Job Safety Analysis?
For those interested in a simple job safety analysis definition, this is the procedure that allows specific job operations to become safer by integrating certain safety and health principles. Not only are potential and actual hazards identified through this analysis, but recommendations are also developed to help ensure that risks are minimized, if not entirely eliminated. When it comes to the medium or platform, there are several options to go for. For example, all of this can be done through a job safety analysis worksheet or perhaps through a job safety analysis powerpoint presentation.
Tips for Conducting a Job Safety Analysis
Even with the many commonalities, it is highly unlikely for job safety analysis examples to be too similar. The job safety analysis steps and the job safety analysis form may be similar, but key differences will take place depending on the circumstances and the manner of execution. To help make the process easier for you, here are four important tips:
Tip 1: Always Involve the Employees
Since they are the ones who are involved in the company’s day-to-day operations, it is always a good idea to gain the cooperation of the employees. They must also be informed of the goals and objectives of the analysis so that they can add to the process, rather than detract from it. Some may have insights to provide, so interviews will definitely come in handy.
Tip 2: Carefully Review the Company’s Accident History
Learning about the company’s history of not just accidents, but also illnesses and near-misses. Doing so will provide you with enough information on what to look out for. Future accidents become easier to anticipate, which means safety risk measures also become easier to apply.
Tip 3: Looking into the OSHA Standards and Requirements
There are numerous standards and requirements that apply to a variety of scenarios. You may find the company in need of those in some shape or form. Having reviewed the company and discussed your goals with the employees, now comes the time to look into the OSHA standards that best suits you.
Tip 4: Prioritize on Specific Areas of the Job
Now that you’ve looked into the OSHA standards, one last tip would be to choose which jobs to prioritize. It helps to go for jobs that have the highest counts of injuries and illnesses. Any jobs with more than one ‘close calls’ are also highly recommended. It may also be worth prioritizing jobs that are complex and in need of written instructions from management.
FAQs
What are the different stages of job safety analysis?
The first stage to concern oneself with is selecting the jobs that require the analysis. The second step is breaking that job down into defined sequences. Third, one must identify the potential hazards posed by the jobs. Lastly, one must develop preventive measures that can either eliminate or at least reduce the hazards.
What are the benefits of performing a job safety analysis?
Besides making certain jobs much safer to perform, there are other benefits to reap from conducting this analysis. One would be the increase in knowledge regarding the job. Operations become more nuanced and innovations are right around the corner. Another benefit is that the results can help serve as a treading program aid for future workers and the management as a whole.
What are the most common types of hazards?
According to the Occupational Safety and Health Administration, there are at least five workplace hazard types. First, there is a safety hazard. Then there is a chemical hazard, followed by biological hazards, physical hazards, and ergonomic hazards.
Safety is often preceded by proper preparations. Conducting hazard assessments and job safety analysis are among the things that any responsible company owner can do to ensure that everyone within the organization is kept safe. Now that you’re better aware of what a job safety analysis is, what will you do? Take heart and be assured over the fact that your new-found knowledge now makes your chances of success that much higher.
17+ Job Safety Analysis Examples to Download
As much as we’d all like to work in perpetually safe environments, that’s not really the case. There will be hazards from time to time, but companies must find ways to mitigate those for everybody’s benefit. To help out with that endeavor, it comes highly recommended that companies conduct their own job safety analysis from time to time. Learn more about it by scrolling down and check out what a top-notch job safety analysis template looks like from our list below.
Job Safety Analysis examples
Details
File Format
Google Docs
MS Word
Pages
Editable PDF
Size: A4, US
Job Safety Analysis Spreadsheet Template
Details
File Format
Excel
MS Word
Apple Numbers
Apple Pages
Size: 33 KB
Job Analysis Gantt Chart Template
Details
File Format
Excel
Size: 28 KB
Safety Analysis Report Template
Details
File Format
MS Word
Google Docs
Apple Pages
PDF
Size: 118 KB
Job Analysis Report Template
Details
File Format
MS Word
Google Docs
Apple Pages
PDF
Size: 29 KB
Job Safety Analysis Template
Details
File Format
Pages
MS Word
Size: A4, US
Job Safety Analysis Worksheet Example
aujsa.com
Details
File Format
PDF
Size: 50 KB
Job Safety Analysis Worksheet Template
aujsa.com
Details
File Format
PDF
Size: 57 KB
Job Safety Analysis Document Example
portablegasgrillweber.com
Details
File Format
PDF
Size: 299 KB
Task Specific Job Hazard Analysis
portablegasgrillweber.com
Details
File Format
PDF
Size: 115 KB
Sample Job Task Analysis Form
confessionsofasecretshopper.com
Details
File Format
PDF
Size: 155 KB
Job Safety Analysis Template
portablegasgrillweber.com
Details
File Format
PDF
Size: 65 KB
Field Level Job Risk Assessment
update234.com
Details
File Format
PDF
Size: 96 KB
Job Hazard Identification Checklist
slideshare.net
Details
File Format
PDF
Size: 72 KB
Job Safety Analysis Worksheet Document Example
rezofthestory.com
Details
File Format
PDF
Size: 160 KB
Construction Risks Job Safety Analysis
beneficialholdings.info
Details
File Format
PDF
Size: 71 KB
Generic Job Safety Analysis Form
evpatoria.info
Details
File Format
PDF
Size: 71 KB
What Is a Job Safety Analysis?
For those interested in a simple job safety analysis definition, this is the procedure that allows specific job operations to become safer by integrating certain safety and health principles. Not only are potential and actual hazards identified through this analysis, but recommendations are also developed to help ensure that risks are minimized, if not entirely eliminated. When it comes to the medium or platform, there are several options to go for. For example, all of this can be done through a job safety analysis worksheet or perhaps through a job safety analysis powerpoint presentation.
Tips for Conducting a Job Safety Analysis
Even with the many commonalities, it is highly unlikely for job safety analysis examples to be too similar. The job safety analysis steps and the job safety analysis form may be similar, but key differences will take place depending on the circumstances and the manner of execution. To help make the process easier for you, here are four important tips:
Tip 1: Always Involve the Employees
Since they are the ones who are involved in the company’s day-to-day operations, it is always a good idea to gain the cooperation of the employees. They must also be informed of the goals and objectives of the analysis so that they can add to the process, rather than detract from it. Some may have insights to provide, so interviews will definitely come in handy.
Tip 2: Carefully Review the Company’s Accident History
Learning about the company’s history of not just accidents, but also illnesses and near-misses. Doing so will provide you with enough information on what to look out for. Future accidents become easier to anticipate, which means safety risk measures also become easier to apply.
Tip 3: Looking into the OSHA Standards and Requirements
There are numerous standards and requirements that apply to a variety of scenarios. You may find the company in need of those in some shape or form. Having reviewed the company and discussed your goals with the employees, now comes the time to look into the OSHA standards that best suits you.
Tip 4: Prioritize on Specific Areas of the Job
Now that you’ve looked into the OSHA standards, one last tip would be to choose which jobs to prioritize. It helps to go for jobs that have the highest counts of injuries and illnesses. Any jobs with more than one ‘close calls’ are also highly recommended. It may also be worth prioritizing jobs that are complex and in need of written instructions from management.
FAQs
What are the different stages of job safety analysis?
The first stage to concern oneself with is selecting the jobs that require the analysis. The second step is breaking that job down into defined sequences. Third, one must identify the potential hazards posed by the jobs. Lastly, one must develop preventive measures that can either eliminate or at least reduce the hazards.
What are the benefits of performing a job safety analysis?
Besides making certain jobs much safer to perform, there are other benefits to reap from conducting this analysis. One would be the increase in knowledge regarding the job. Operations become more nuanced and innovations are right around the corner. Another benefit is that the results can help serve as a treading program aid for future workers and the management as a whole.
What are the most common types of hazards?
According to the Occupational Safety and Health Administration, there are at least five workplace hazard types. First, there is a safety hazard. Then there is a chemical hazard, followed by biological hazards, physical hazards, and ergonomic hazards.
Safety is often preceded by proper preparations. Conducting hazard assessments and job safety analysis are among the things that any responsible company owner can do to ensure that everyone within the organization is kept safe. Now that you’re better aware of what a job safety analysis is, what will you do? Take heart and be assured over the fact that your new-found knowledge now makes your chances of success that much higher.